Technology and machinery
Design
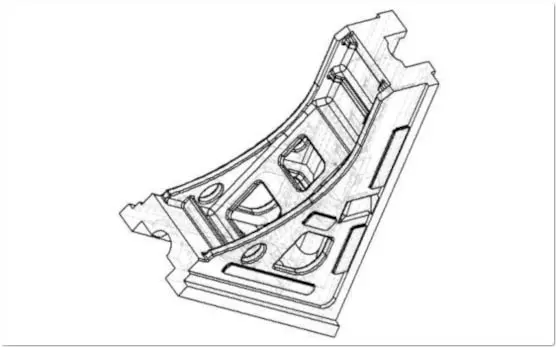
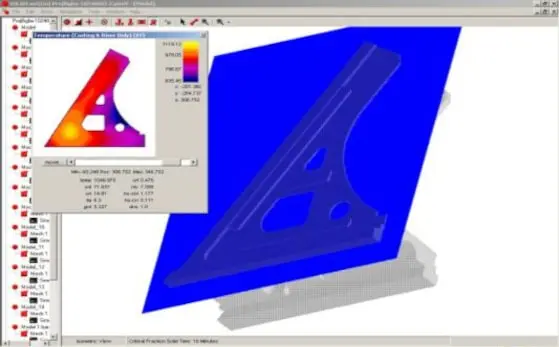
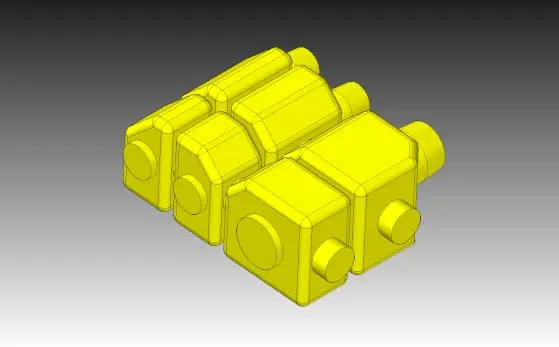
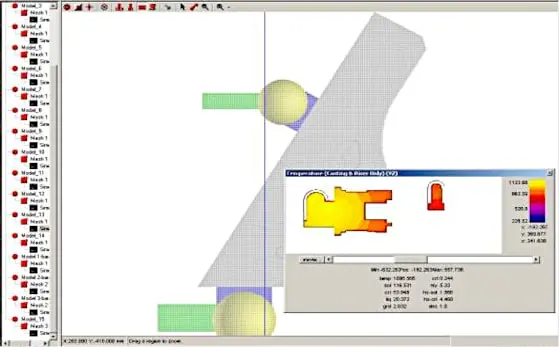
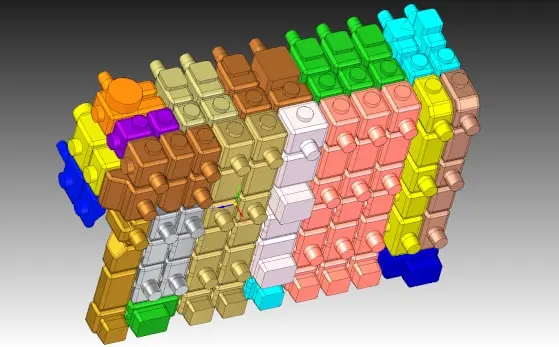
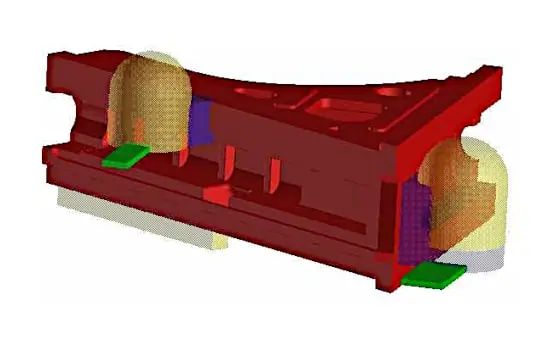
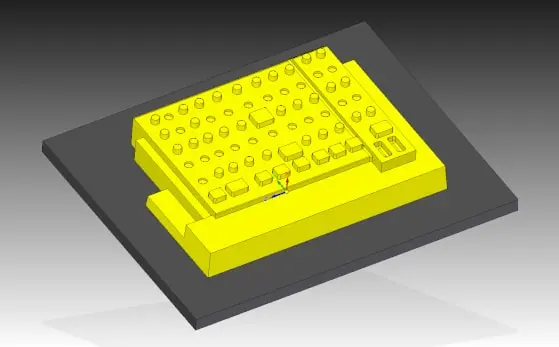
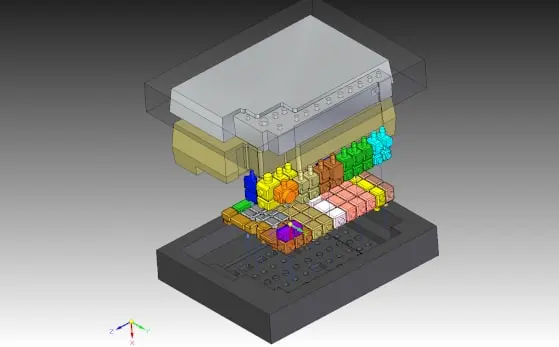
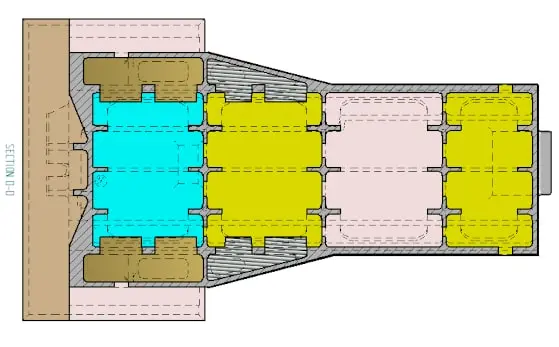
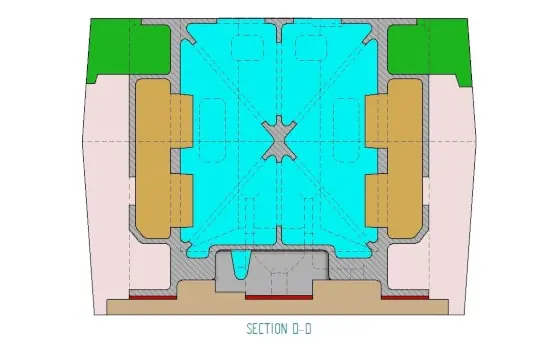
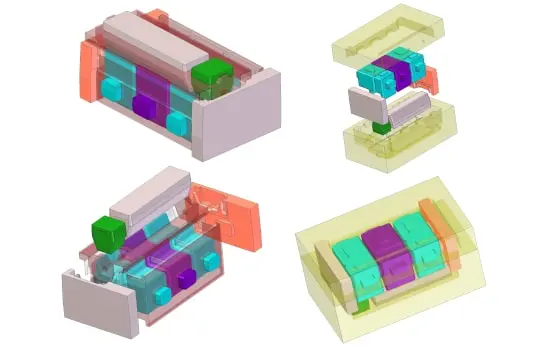
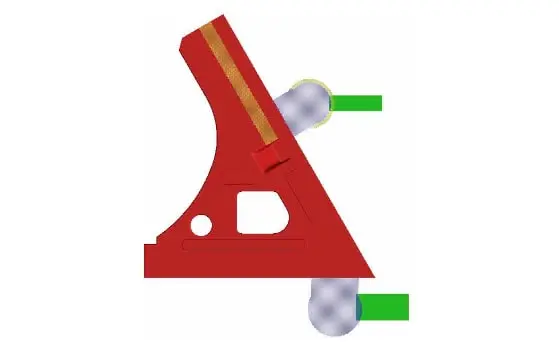

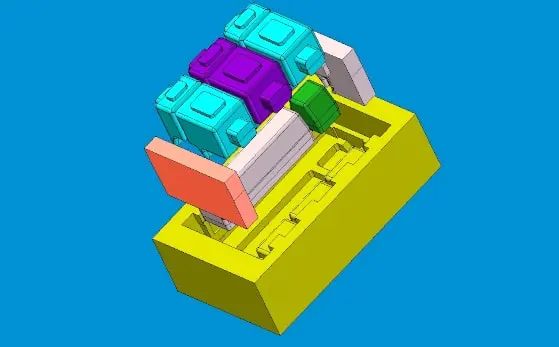
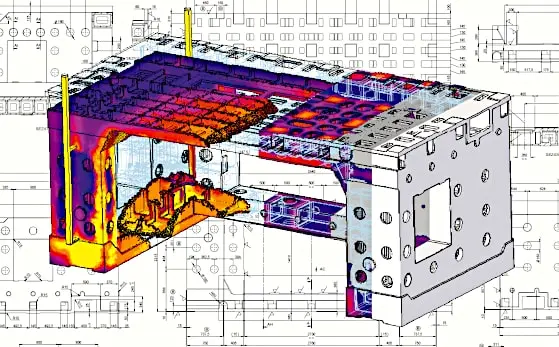
Engineers with great experience in the development of casting technologies work in the Design department. Our objective is to obtain castings that fully meet the customer's requirements, as well as a good streamline of the production process. We use CAD-CAM-CAE design stations and systems, with the possibility of accessing several 2D and 3D formats.
The pattern shop
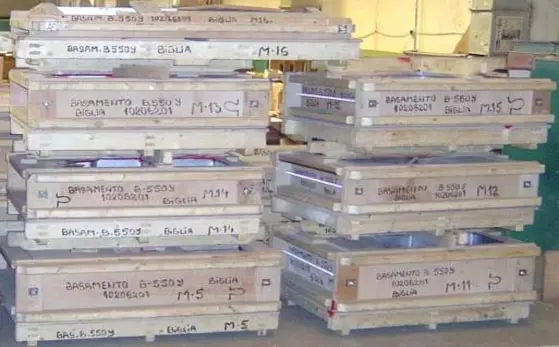

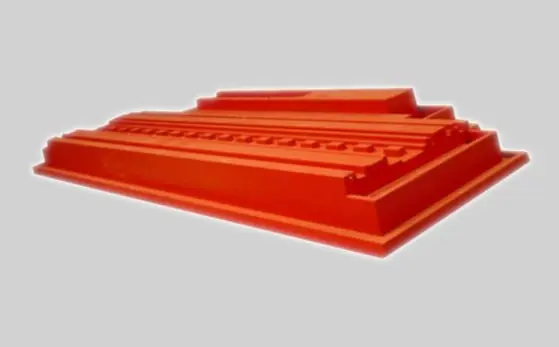

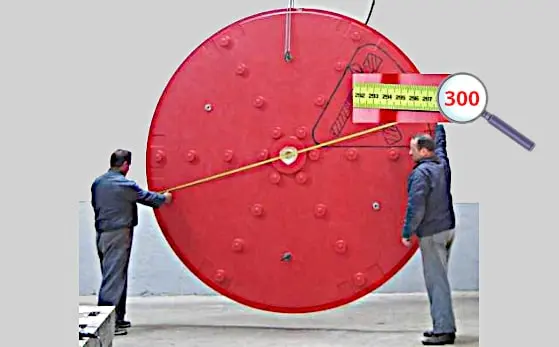
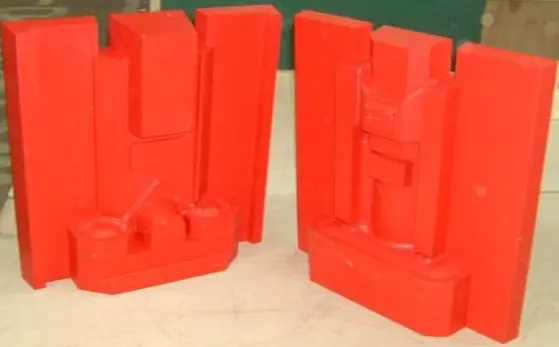
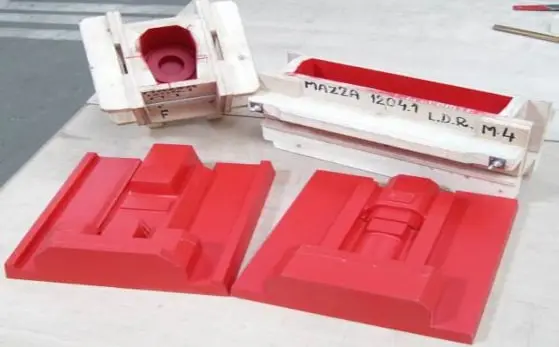
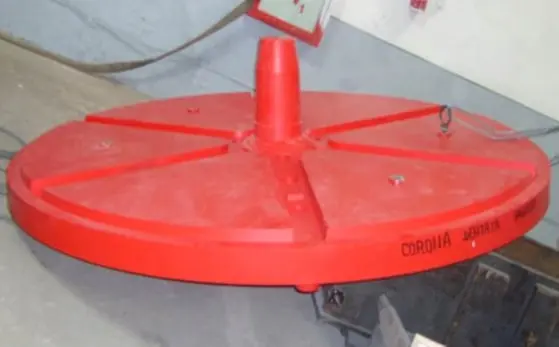
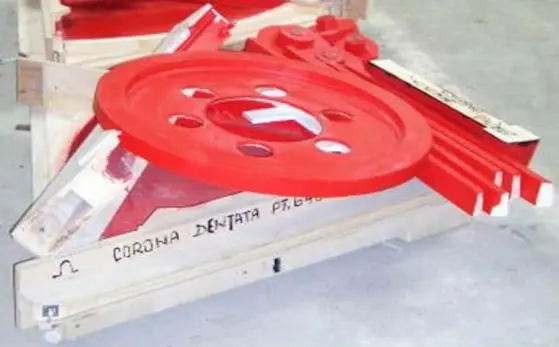
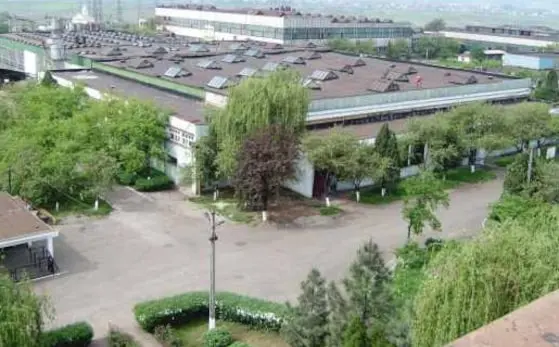
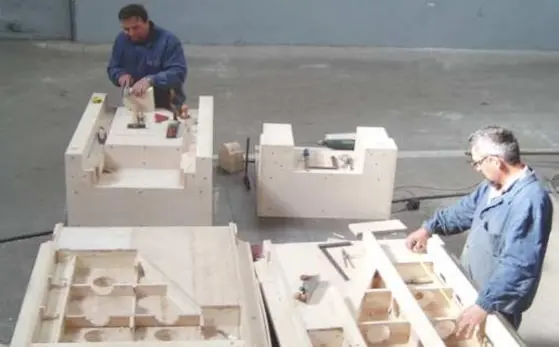

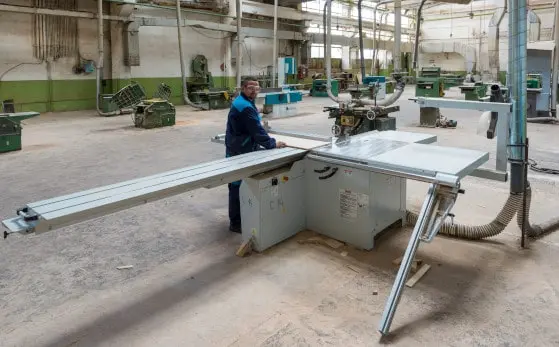
SATURN S.A. is specialized in manufacturing complete pattern equipments of wood, building all patterns required for our own production, regardless the castings complexity.
High quality materials are used, like beech multilayed wood.
The technology and materials enable patterns to have precise dimensions, dimensional stability in time and durability in operation during serial production.
The patterns and core boxes are stored under best conditions in covered storehouses, equipped with fire protection and production integrated data base.
Foundry
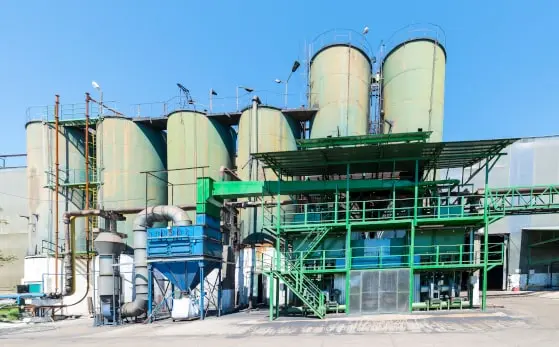
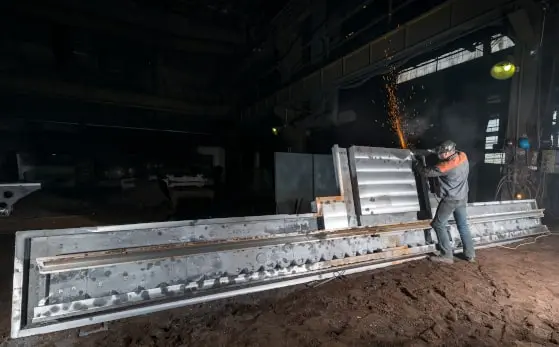
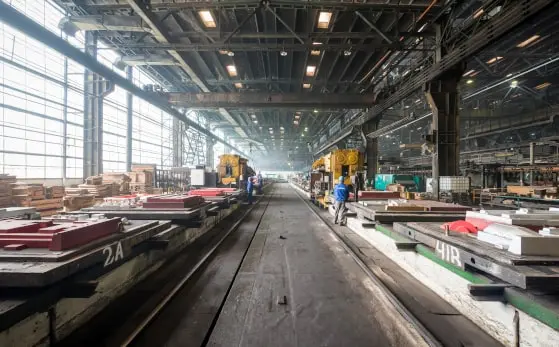
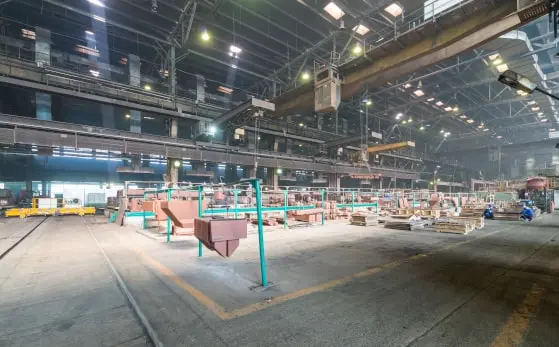
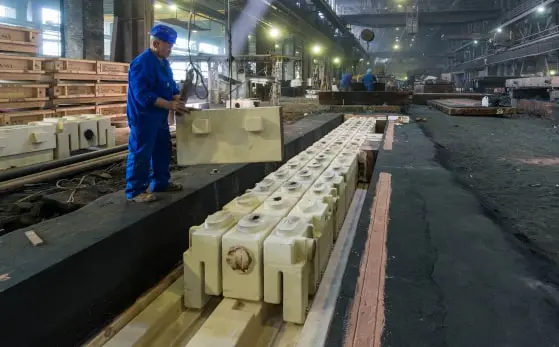

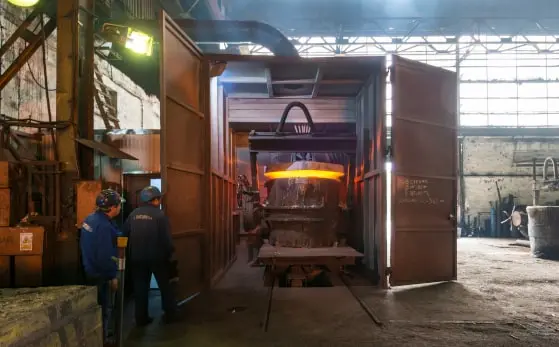
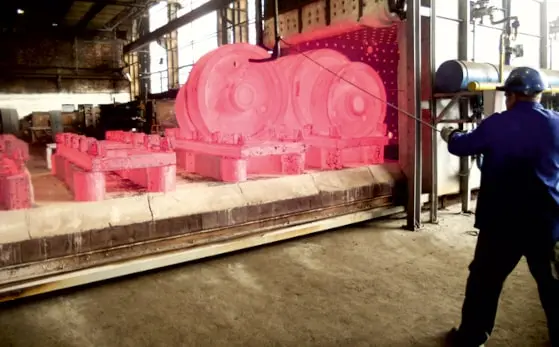
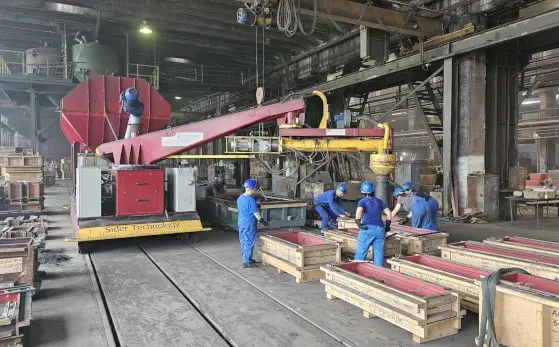
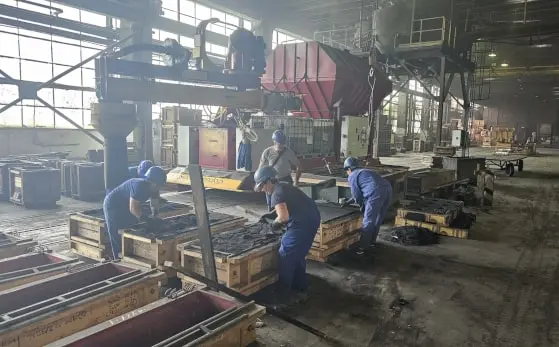
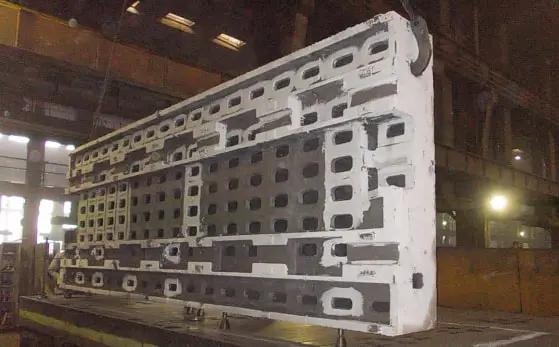
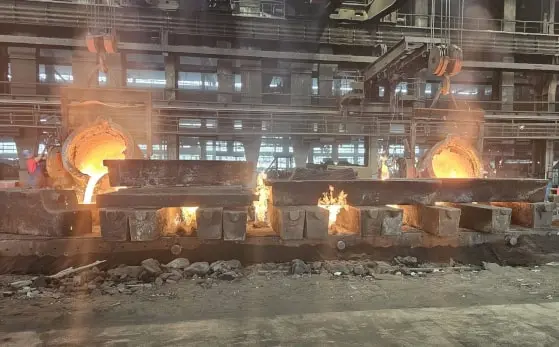
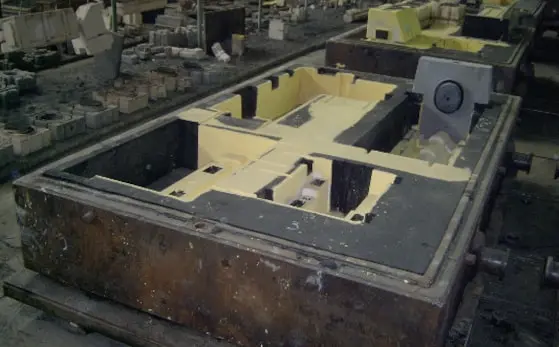
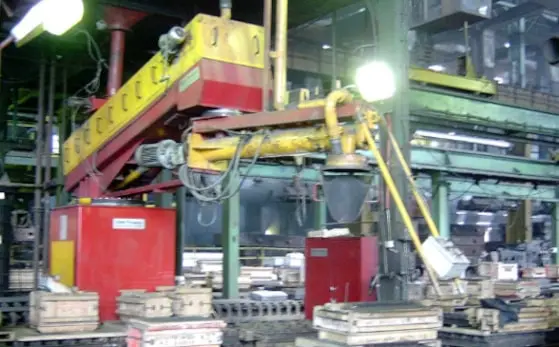
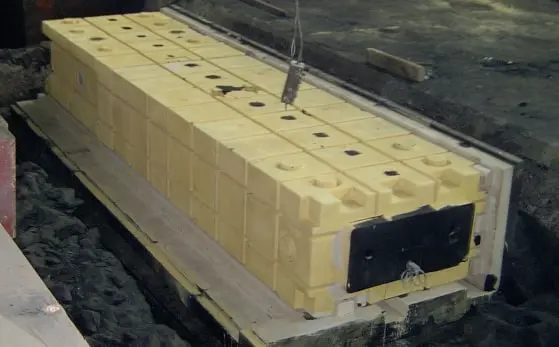
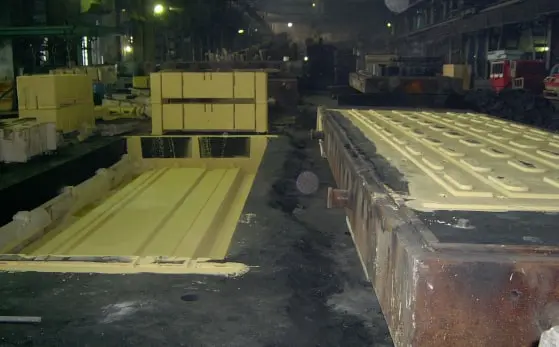
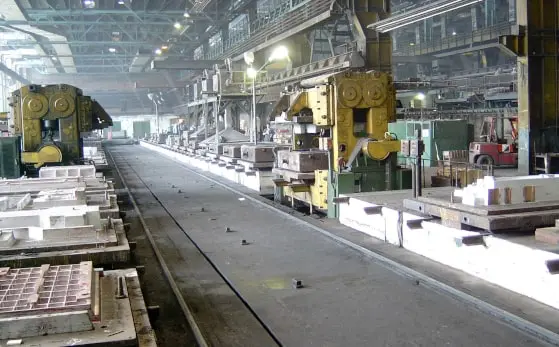
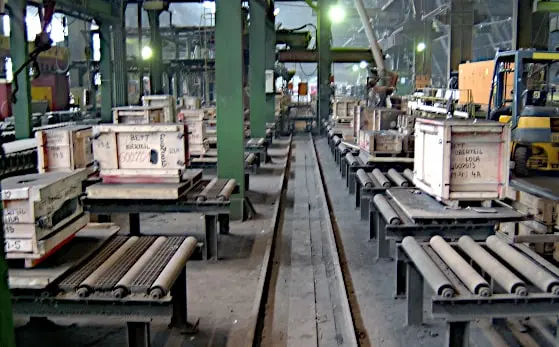
The Foundry has the following production facilities:
Molding Zone
- We use only phuran resin molding sand realized by highly productive mixers.
- There are two mechanized lines for castings up to 10.000 [Kg]. We use molding flasks sized 2400x1600x200÷500[mm] respectively 4000x2400x200÷700[mm].
- The mechanized molding lines are equipped with carts to transfer the molding flasks between the different workstations: forming stations with vibrating tables, machines for extracting the patterns from the molds, molds painting stations, cores mounting stations, molds closure machine.
- One manually performed line for castings up to 40.000 [Kg]. We use oversized molding flasks for pit molding.
- Each molding line has its own cores molding shop.
Cast iron elaboration area
- Three crucible induction furnaces of 12.5 tons each.
- Two maintenance induction furnaces of 55 tons each.
- Equipment for rapid chemical analysis.
- Mg wire modification plant for nodular cast iron production.
- Program for thermal analysis of cooling curves.
Cleaning place
- Two vibrating debate installations.
- hree sandblasting installations with metallic shots.
Heat treatments
- Stress relieving: parts up to 35,000 [Kg], maximum dimensions: 8000x3000x1700 [mm].
- Normalization for castings with special requirements.
Mechanical Processing Section
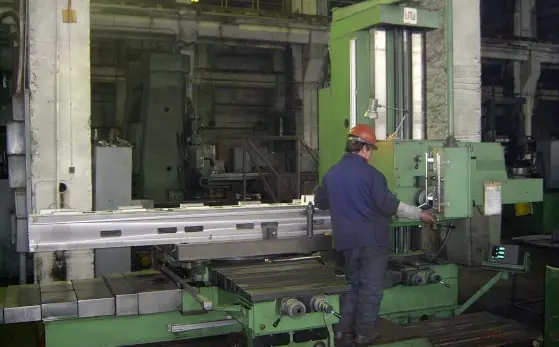
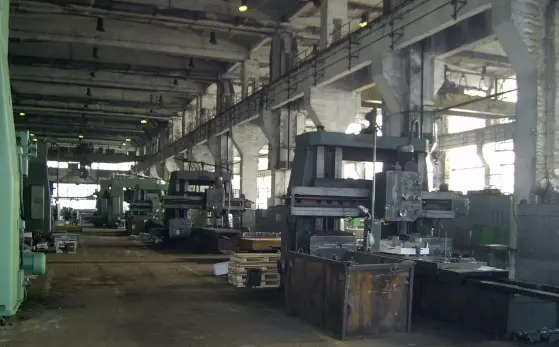
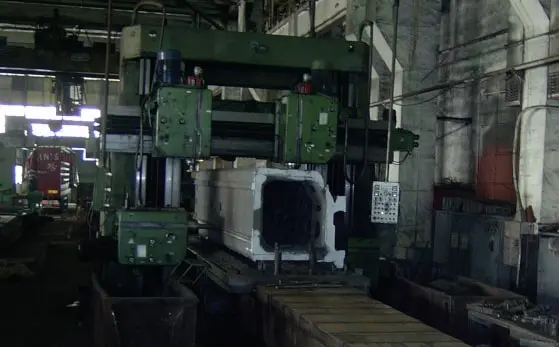
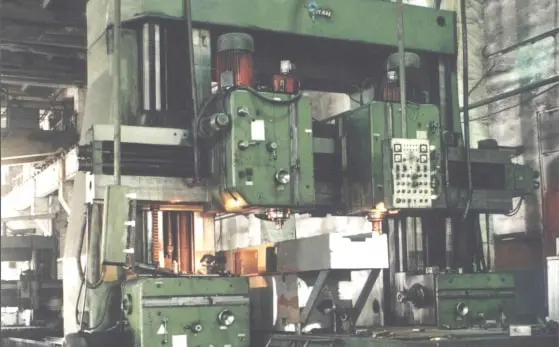
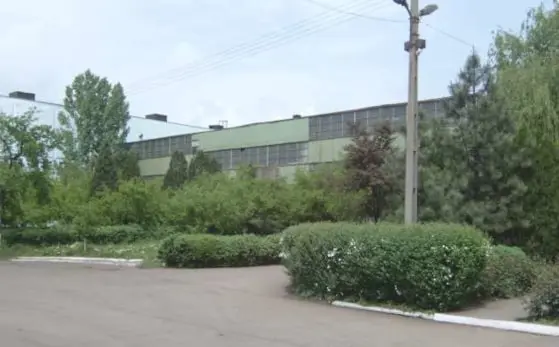
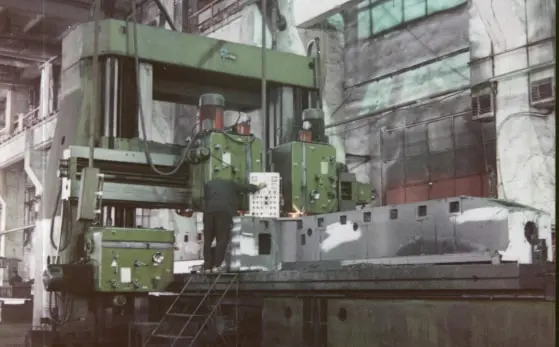
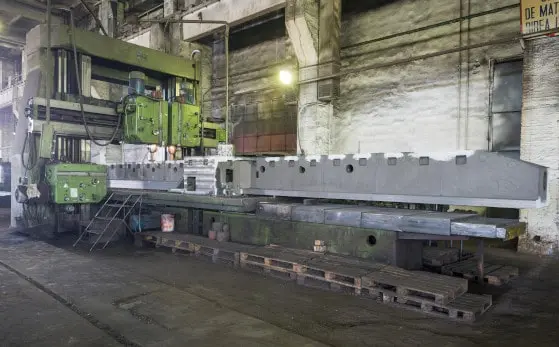
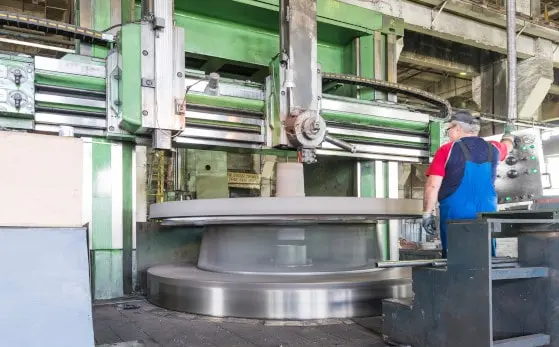
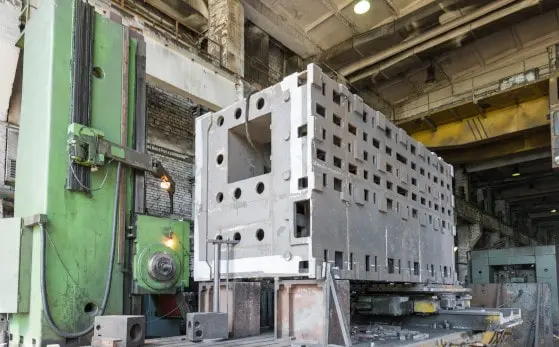
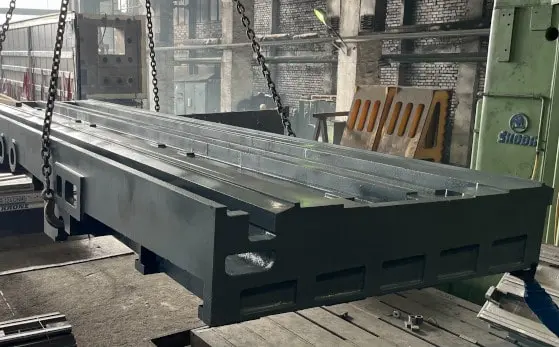
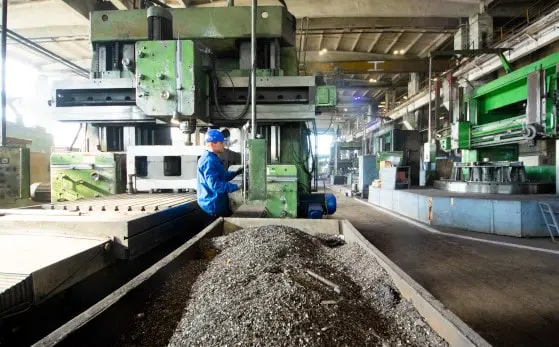
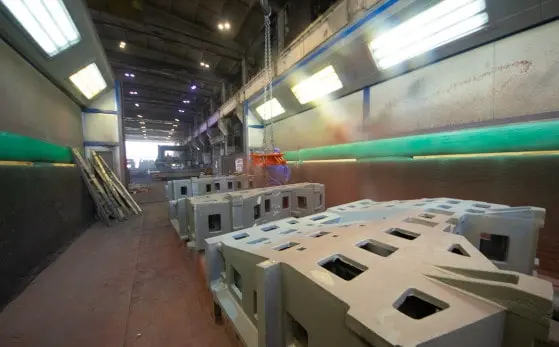
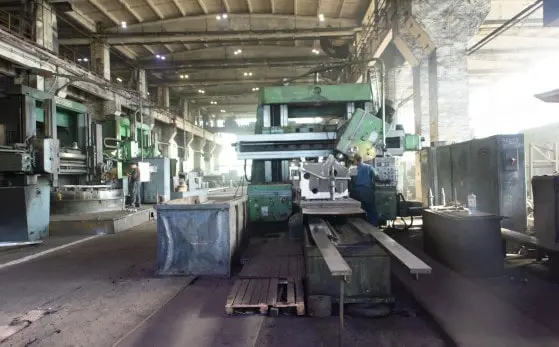
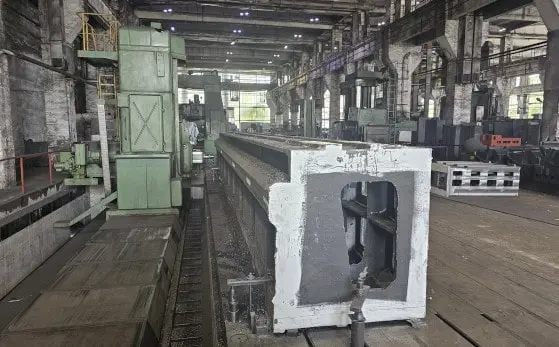
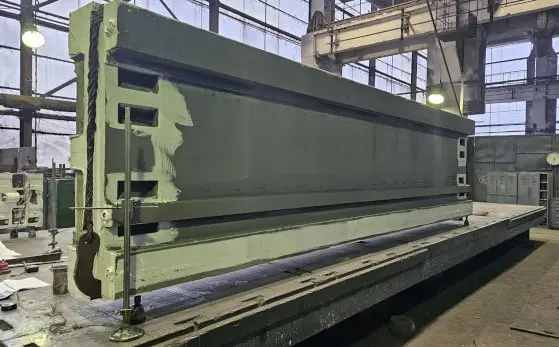
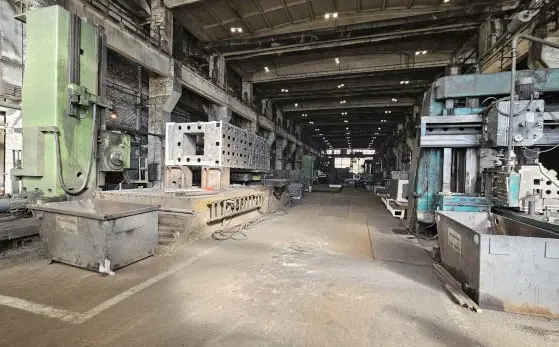
The Mechanical Processing Section is equipped with robust machine tools, suitable for performing rough-machining operations.
- Universal lathes;
- Carousel lathes – SC1600; SC2500; SC2700;
- Universal milling machines (FUS);
- Milling machines with portal type FLP660; FLP1000; FLP2000 on which we can process parts with mass up to 16 To and lengths of 9,000 mm;
- Boring and milling machines type AF85; AFD100; AFM150; AFL150 on which parts with mass up to 20 To and lengths of 13,000 mm can be machined.
The priming plant is used to protect cast parts against corrosion.